Haylage
Haylage is made using conventional round or medium square balers to package high moisture forage. The forage is then enclosed in a plastic cover, bag, wrap or tube to exclude oxygen to complete the fermentation process.
Haylage systems are very flexible, have low capital requirement, and low labour requirements. They also lower fuel costs, compared to chopped silage, while offering the potential reduction in dry matter and weather losses that silage systems offer. However, the variable costs are high, due to the cost of the plastic required to seal the haylage; and spoilage in the system can be high if care is not taken to adequately seal out oxygen during the wrapping process and during storage.
Disposal of used plastic is also a problem. Haylage can and should be fed in conventional round bale feeders, to reduce wastage.
Forage can be cut and conditioned in the same manner that a hay crop is harvested. The crop is field wilted to 40 to 60 per cent moisture and then baled. Baling forage at the correct moisture content is important - baling material that is too dry will result in poor fermentation and increased storage losses, and baling too wet reduces the amount of dry matter stored in each bale, thereby increasing costs.
Haylage can be produced using baling equipment that can produce a bale with a weight of 590 to 730 kilograms (1300 to 1600 lbs). See Table 1. Bales heavier than 730 kg (1600 lb.) put excessive strain on baling and handling equipment and are unsafe to handle. Round bales 1.5 m (4 to 5 ft.) in diameter and 50 per cent dry matter weigh approximately 900 kg (2000 lb.). Some balers may require modifications to make round bale silage. Bales should be encased in plastic as soon as possible after baling to maintain quality.
Table 1. Effect of bale diameter and moisture content on bale weight kg (lb.)
Bale diameter ft. |
Moisture % |
|||
30 | 40 | 55 | 65 | |
4 | 364 (800) | 482 (1,060) | 636 (1,400) | 818 (1,800) |
5 | 454 (1,000) | 591 (1,300) | 773 (1,700) | 1045 (2,300) |
6 | 568 (1,250) | 727 (1,600) | 1000 (2,200) | 1273 (2,800) |
Source: Manitoba Agriculture, Food and Rural Initiatives
The bagging process involves elevating the bale and pulling the bag over the bale. The bag is then pulled tight and double tied. Placing the bales in the bags, excluding air and moving bales into storage is challenging work.
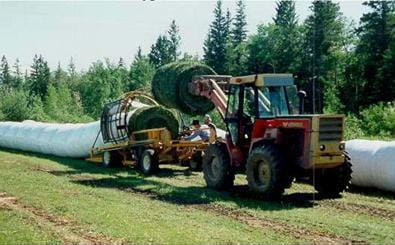
Bale wrapping involves using a bale-wrapping machine to encase the bale in one mil plastic. Generally, the plastic should be overlapped 50 per cent to ensure an airtight seal and wrapped twice. The plastic is stretched 50 to 55 per cent to attain the desired tension.
Round bales can also be stored in plastic tubes by using shop built or commercially produced equipment. In either case, a ring holds the end of the plastic tube, and is moved ahead to pull the plastic over the next bale. Securing loose plastic is important to reduce tears and subsequent haylage spoilage.
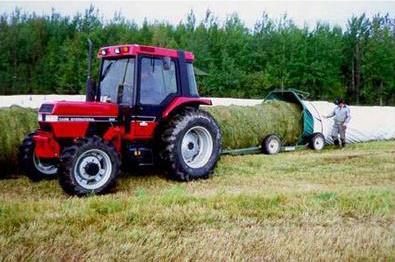
Round bales can also be stacked and covered with plastic. A 13 X 33 m (40 X 100 ft.) plastic sheet will cover 100 to 125 round bales stacked in a four-three-two configuration. It is difficult to exclude all of the air in this system, so it has a greater potential for spoilage. A shop vacuum can be used to remove air from beneath the cover.
Spoilage will rapidly occur in the remaining silage when the cover is removed during warm weather for feeding. Therefore, covered bale silage is best fed during winter. To avoid freezing of bales during winter, only remove and feed what will be consumed within a couple of days.
Air cannot be totally excluded in any of the bale silage storage techniques; therefore, the fermentation and ending pH level can be quite high, sometimes over five, which makes the silage particularly vulnerable to spoilage (Table 2). The ability of the cover to exclude air is paramount to the successful storage of the silage.
Table 2. pH levels in relation to fermentation period and silage type
Fermentation days |
pH |
|
Bale silage | Chopped silage | |
0 | 5.7 | 5.7 |
1 | 5.78 | 5.1 |
3 | 5.7 | 4.9 |
9 | 5.5 | 4.6 |
60 | 5.1 | 4.4 |
Source: Manitoba Agriculture, Food and Rural Initiatives.
Use only top quality, warrantied UV-resistant plastic products. Generally speaking, plastic products can only be used once, certainly in the case of wrapped bales. Enclose bales as soon as possible after baling to prevent heating of bales. Inspect enclosed silage frequently to detect holes or tears in the covering, and patch with plastic tape designed for that use. Package and store the silage close to where it will be fed on a sloped, well-drained site. Locate rows of bales, or tubes perpendicular to the slope, for enhanced drainage.
Moving bales before they are to be fed may result in damage to the cover and subsequent spoilage; indeed some storage methods, such as tubes, cannot be moved after they are filled. Remove all surface irregularities from the storage site and remove vegetation and weeds, to reduce damage to plastic and rodent infestations.